Trusted designers and builders of gold standard energy efficient buildings
PASSIVHAUS
A DESIGN & BUILD SERVICE
You want your building to be the most energy efficient it can possibly be; Passivhaus is how you know that it is.
Passivhaus is the most exacting building performance standard there is. It’s a rigorous set of guidelines that dictate how a building should be designed and built in order to achieve the most efficient energy-use performance possible.
A Passivhaus building delivers ultimate comfort and long-term cost savings. It requires minimal heating and cooling, meaning low energy bills and high temperature consistency.
We’re experienced Passivhaus designers who have delivered certified Passivhaus newbuilds and EnerPHit standard retrofits. Our air tightness results are always exemplary, reassuring you that we always deliver what we promise.
We’re committed to offering our clients the best in sustainable design and construction. Working to Passivhaus standard is proof that we are as good at what we do as we say we are.
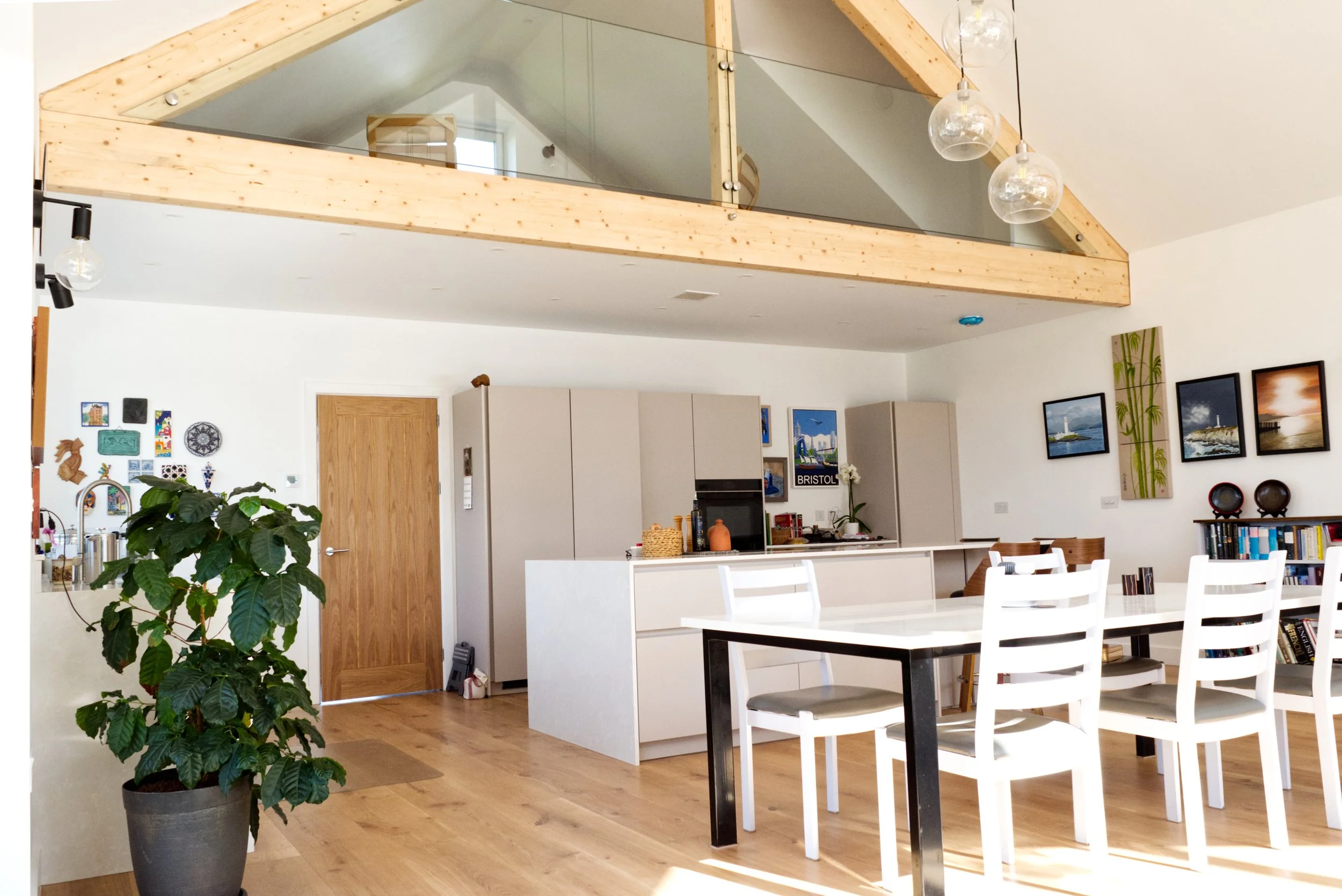
Beautiful, elegant, uncluttered design
The Passivhaus building standard informs design from the earliest stages. It’s not something that can be easily tagged on to a project later, like solar panels.
When beginning your Passivhaus project, we’ll work with you to carefully assess the natural advantages and challenges of your site. We’ll first identify the optimum position, orientation, shape and shading of your new building. Function inspires form in Passivhaus design: the more complicated the shape, the less energy efficient it will be.
At Greenacre we embrace the beauty of simple, uncluttered design in our Passivhaus projects to optimise performance. Our goal is to create ultra low-energy buildings that are easy to maintain and a joy to be in.
The burden of proof: excellence in construction delivers air-tight results
A Passivhaus build always follows the same steps to make sure the results are consistently excellent. Our process is checked by an independent Passivhaus certifier.
In the design stage we’ll use Passivhaus Planning Package (PHPP) software to create a bespoke thermal model for your project. This highly detailed spreadsheet allows us to test variables such as different materials, insulation build-ups, layouts and openings to find the optimum configuration for your building and budget.
To achieve such a high level of energy efficiency, Passivhaus buildings must be completely free from draughts - and so avoid the heat loss associated with warm air constantly leaking out of the building. A Mechanical Heat Recovery and Ventilation (MVHR) system will be installed to provide whole-house ventilation without cooling your house like draughts do. Windows can still be opened as much as you like, but the MVHR will continue to silently and efficiently do its job in the background.
But how can you know for sure that all that careful design work and meticulous construction paid off? - that your building really is as good as we promised it would be?
This is where the air tightness test comes in.
During construction an independent certifier will check our work to make sure we’re building what we designed. Our experienced builders will also be making sure there are no holes in your building’s fabric. Every junction, every opening, is carefully sealed with air tightness tape - making sure there are absolutely no draughts.
An independent tester will conduct an air tightness test at the end of the first fix of construction and again at the end of the project. This is where we close all the windows and attach a huge fan to the front door which then measures how ‘air-tight’ the building is. This in turn will demonstrate that the building is sealed and therefore temperature controlled.
For a new build Passivhaus the air tightness result has to be below 0.6 ach @ 50 pascals. We consistently get excellent air tightness results and have had readings as low as 0.27 ach @ 50 pascals.
We cant stress how important these results are when choosing a Passivhaus designer and contractor - because at the end of the day, no matter how nice the design or how hard everyone worked, if you get a poor air tightness result then your building won’t pass the Passivhaus standard.
Aside from not getting the badge, it’s a terrible dissapointment to have a poorly performing building when you thought you’d invested in the opposite.
The many benefits of a Passivhaus build
Everyone has their own reasons to pursue a Passivhaus project. Some may prioritise sustainability and see Passivhaus as a means to doing the most they can for the environment. Others may prioritise long term low-energy bills and personal security in the face of climate and energy price uncertainty. Still others may worry more about internal air quality and avoidance of problems like mould or damp.
But many may not realise just what a joy Passivhaus spaces are to be in. They have a wonderfully consistent temperature, making them warm in winter and cool in summer. High surface temperatures and excellent humidity regulation make the building feel warmer even than it is.
The are so many advantages to a Passivhaus build that we now approach all our new builds with Passivhaus design principles regardless of whether our client wants to work towards independent certification.
When you know how good a building can be, why settle for anything less?
Natural materials and Passivhaus.
We use natural materials wherever possible in all our projects, including Passivhaus buildings.
Some people may think that modern highly engineered materials would offer superior performance over natural materials, particularly in an ultra-low energy Passivhaus, but we find the opposite is usually true.
As well as being better for the environment and safer to work with, natural materials offer extra advantages such as flexibility and breathability. They are usually naturally ‘vapour open’ materials, meaning they don’t trap water and damp like some popular modern synthetic materials.
A standard Greenacre construction build up for Passivhaus new builds is timber frame, wood fibreboard, recycled newspaper Warmcell blown insulation, lime render, timber cladding and slate tiles - all of which are natural materials.
Internally we recommend finishing all plasterwork with natural clay-based paints and natural oil finishes on woodwork rather than varnishes.
All these materials have a natural beauty as well as being non-toxic to internal air quality.
“Dan managed the project throughout the construction on a tight and complex site. We were targeting EnerPHit and it was a great relief knowing that Dan understood and was able to achieve the quality control of the build.”
Sally Godber - Hutong Cafe & Flat, Passivhaus Retrofit
-
Your Passivhaus journey with us will start with a chat on the phone followed by an initial meeting with our director on-site at your building to discuss your ideas. This first contact is always free and no-obligation.
-
This first stage is where we take time to understand what you really want. We’ll carefully consider your goals and aspirations for the project, how much it might cost and what constraints the project may face along the way.
We’ll look into any potential planning permission or land use challenges and conduct a thorough feasibility assessment. At the end of this stage we’ll give you a cost estimate for both the design and construction phases of the whole project.
-
This is where your design starts to really take shape. Using the information gathering in the previous stage we’ll work up some initial design options for discussion. We’ll involve you closely in developing your initial ideas into a final design you love.
We’ll then work with you to refine this vision into an application for planning permission. We’ll manage this process for you, liaising with engineers, specialists and independent planning consultants where needed, to make sure the process is as easy as possible.
At the end of this stage we’ll give you an updated cost estimate for the second stage of design as well as the project build.
-
Once planning permission has been approved we will then develop your design further to include all relevant detail needed to actually build your project.
In this stage we create highly detailed technical plans that specify everything we’ll need to know in order to actually build your project. Materials, finishes, windows and structural loading are all things that will be finalised now. As part of the design process for Passivhaus we’ll also build a PHPP thermal model so we can optimise the design of your building.
At the end of this stage we will give you a final cost estimate for the build.
-
We’ll prepare a contract, secure building control approval and make all last preparations for the build.
The construction process itself will be a seamless onward process from the design stage. We will manage everything ourselves and continue to involve you closely as the build progresses so you always know what’s going on.
-
At the end of the build we will conduct a final air tightness test in order to secure Passivhaus certification.
When this process is complete you will receive your formal Passivhaus certification and a badge you can proudly display on your house.
-
We will make sure that final building control approval is secured and the building warranty is complete.
As we handover your beautiful new building we’ll be on hand to address any concerns or questions you may have. We’ll make sure you understand what to expect from your new building and that you have all the information you need to feel confident taking over management of it.
Our Process - Passivhaus
Selected projects
Ready to talk over your Passivhaus project?
Give us a call or drop us an email to start the conversation about your Passivhaus project.
Any initial chat or consultation is always free and no-obligation.